PADDLE DRYER
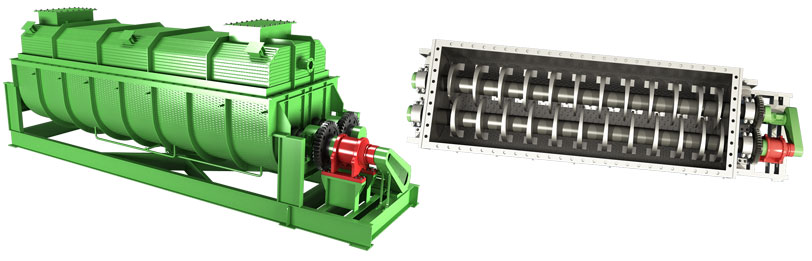
INTRODUCTION:
Star Trace is one of the leading and reputed manufacturing company in India with 25 years experienced in this field. Star Trace Paddle Dryer designed and manufactured can efficiently dry all kinds of sludge by utilizing steam or heat conduction oil as heat source.
Working Principle:
The paddle dryer for drying or cooling of paste, particle, powder and slurry state of material, perform the process of drying, cooling, heating, sterilizing, reacting and combustion under low temperature. The special stirring and heating transferring blade, makes high heat transferring efficiency, and provide self-cleaning function. The special chock shaped stirring and heat transferring blade has high heating efficiency and self-cleaning function of the heating transferring surface.
Hollow chock shaped blades are concentrated on the hollow shaft. Heat media flow through the blade from the hollow shaft. The heat transferring area in the effective volume is very high. The temperature range of heating media is -40 °C to 320 °C . It might be steam, or liquid state, such as steam, thermal oil etc. Indirect heating, there's no heat carried out by air. All heat is utilized for to drying the material except the lost of heat insulation layers. The surface of chock shaped blade has self-cleaning function. The relative movements of the product particles and the chocked shaped surface might clean the material attached to the chock shaped surface, so to keep the cleanliness of heat transferring surface during working. The shell of hollow blade dryer is Ω shape. 2 or 4 pieces of hollow stirring shaft are usually equipped in the shell. To avoid any leakage of material, there're sealed terminal cover and top cover with the shell. The heat transferring media flow through the rotation connector, jacket's shell and hollow stirring shaft. To ensure best transferring effect, the hollow stirring shaft adopts different interior structure in accordance with different heating media.
Features:
- The heat consumption of blade is low;
- The cost of the blade dryer is low;
- The range of material to be processed is wide;
- The pollution is less: Without any carrying air, very few powder is carried out;
- The operation cost is low;
- Steady operation: The material particles fully contact heat transferring surface, because of the special compressing and swell-stirring effect of the chock shaped blade. The difference of the temperature, humidity and mixing effect are very small in the different axial area, so to ensure the stability of process.
Application:
The blade dryer is successfully applied in foodstuff, chemical, petrochemical, dyestuff, and industrial mud etc. The heating transferring, cooling and stirring characters enable it to perform the following unit operation: combustion (low temperature), cooling, drying (recovery of solvent), heating (melting), reacting and sterilizing. The stirring blade is heat transferring surface too, so to increase heat transferring area of unit effective volume is increased, and decrease processing time. The chock shaped heat transferring surface has self-cleaning function. Compressing and swell-stirring functions make the material mixed uniformly. The material performs the movement of "piston flow" along the shaft. The difference of the temperature, humidity and mixing effect are very small in the different axial area. The blade dryer is capable to perform combustion under low temperature if we adopt thermal oil as heating media.
Design:
- Heat transfer areas from 60 to over 3000 square feet (5.6 to over 305 square metres) per dryer.
- System capacities for small, medium and large plants.
- Indirectly heated using steam or thermal fluid (hot oil).
- Carbon steel, stainless steel, or alloy construction.
- Abrasion-resistant hard-surface coatings are available.
- Inert process during operation.
- Robust design, designed with high torque and low operating speed.
- No internal parts to adjust or maintain.
- Shafts, bearings, and drive components are designed for long life under adverse conditions, insuring long-term mechanical integrity.