VIBRATING TABLES
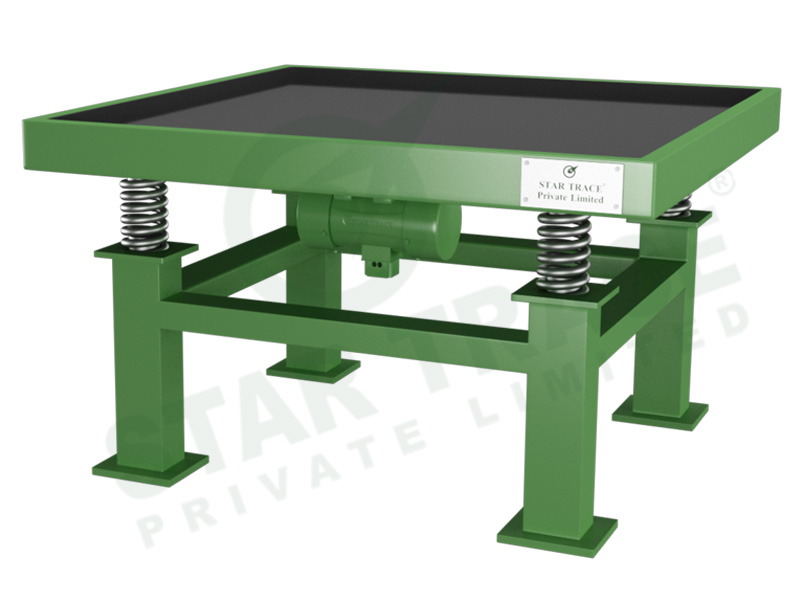
INTRODUCTION:
STAR TRACE Vibrating Tables are designed to settle and compact dry bulk materials in various types of containers. Their application provides either a sizeable increase in the net weight of the container or reducing in the container size with subsequent savings in shipping and storage space.
STAR TRACE Vibrating Tables are available in two types Electromagnetic & Electromechanical. The choice of the proper type and model depends upon the application, characteristics of the material or objects being handled, its reaction to vibration, the maximum weight to be handled and the type of container.
WORKING PRINCIPLE:
Unbalance motors make the table top to oscillate. An oscillation insulating elastic suspension connects the table top and table bottom part. By adjusting the unbalances on the unbalance motors during standstill the oscillation amplitude can be changed. If an electric control with frequency inverter is being used the vibration frequency can be changed even during operation. Both parameter have influence on the vibration intensity and allow an adaption to the different scopes.
INDUSTRIAL USES:
|
|
Features
The following are the features of Vibrating Table:
- User friendly.
- Can hold up to 200lbs.
- High operational efficiency.
- Low power consumption.
- Low on maintenance.
- Noiseless.
- Uniform Vibration.
- Vibration stays on the top plate.
- Trouble free & noiseless operation.
- Properly fitted with the motors and other pars to ensure smooth functioning.
Applications
- Used for compaction, detachment and aeration of bulk materials.
- Used for testing of welded joints in automobile industry and delicate joints in electronic industry.
- Used for effective packing of fluffy and difficult to handle powder in chemical and pharmaceutical industry.
- Used for proper flow of powder in dies and moulds to get perfect moulded parts.
Benefits
- Put more material into smaller containers.
- Ship less air.
- Reduce overflow and spillover waste at filling stations.
- Perform fatigue testing.
- Top quality, fastest delivery.